Robotic Process Automation: Mainstreaming automation in retail, manufacturing and warehouses
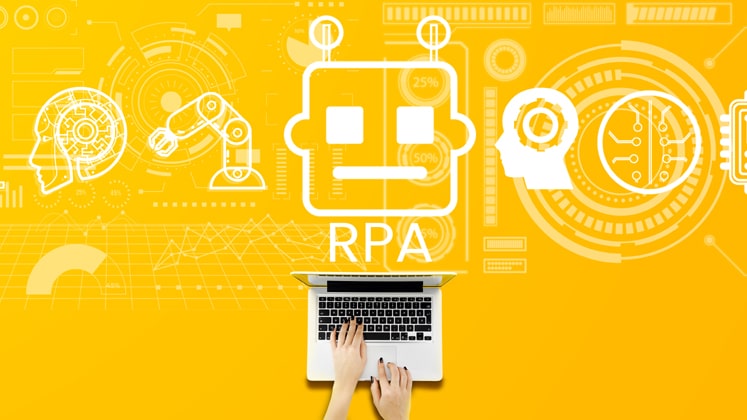
Robotic Process Automation (RPA) has become an essential technology in modern businesses due to its ability to improve efficiency, accuracy and cost savings. As the demand for fast and reliable order fulfilment continues to grow, RPA is now making its space in apparel factories as well.
Reliance Industries Ltd., made huge headlines last year when it acquired Indian robotic automation start-up Addverb (in US $ 132 million) in a bid to adopt greater and more sophisticated levels of robotic automation in its myriad warehouses of a wide range of businesses including its fashion e-commerce wing AJIO.
Much before Reliance took over this robotics company, global e-commerce giant Amazon became the first company to adopt robotic automation at the warehouse level in India as it deployed its in-house robot Kiva to make processes including picking up of a product and packing more efficient than before.
Both the developments are strong indication of the companies’ thrust on the use of robotic automation; however, now the trend is evolving towards ‘Robotic Process Automation’ (RPA) as the retailers, warehouses, factories and e-commerce companies aim at taking care of the supply chain’s agility by deploying Robotic Process Automation bots.
What’s RPA?
Robotic process automation (RPA) is the process of using computer software robots to perform rule-based digital tasks such as data entry, inventory management and order processing, which can save time and increase efficiency. RPA allows fashion businesses and warehouses to assign all their mundane work to machines (bots, to be precise) and concentrate on the work that requires judgment, creativity and interpersonal skills.
Unlike chatbots, which are designed to handle simple queries and interactions, RPA bots interact with any system or application just as humans do. This means they automate a wide range of tasks, from data entry to complex decision-making processes which eventually results in faster and error-free work. With benefits such as greater productivity, better accuracy, ample cost savings, faster ROI, sound integration across platforms and scalability, RPA proves to be the snowball of the fashion industry.
There are two main types of RPA bots: attended bots and unattended bots. Attended bots are designed to work alongside humans, usually in order to help with data entry or other similar tasks. Unattended bots, on the other hand, are designed to work autonomously and can handle more complex tasks such as monitoring stock levels or managing supplier orders.
Approximately 10% to 20% of human work hours are spent on dull and repetitive computer tasks.
RPA expands footprint in apparel factories
RPA has become an essential technology in modern businesses due to its ability to improve efficiency, accuracy and cost savings. As the demand for fast and reliable order fulfilment continues to grow, RPA is now making its space in apparel factories as well.
UiPath robots (RPA-enabled software bot) help South Asia’s largest apparel tech company MAS Holdings to save around 14,000 labour days annually, and taking out chunks of non-productive and repetitive tasks from their employees’ workday has resulted in not only saving man-hours and man-days but also in increasing motivation among the workforce.
“We have extensive front-end processes, including crucial ones for customer service, supply chain management and financial management. Our planned expansion necessitated improved productivity, efficiency and cost savings across the board, all of which could not be accomplished manually. For our digital transformation agenda to have any real effect, we knew that RPA would have to serve as its foundation,” commented Jayantha Peiris, CIO, MAS Holdings.
RPA allows apparel factories today to configure computer software, or a ‘softbot’ to emulate and integrate the actions of a human interacting within digital systems to execute the processes. RPA softbots utilise the user interface to capture data and manipulate applications just like humans do. They interpret, trigger responses and communicate with other systems in order to perform a vast variety of repetitive tasks. Only substantially better: an RPA softbot never sleeps and makes zero mistakes.
RPA can analyse historical sales data to predict future demand for specific products. This enables inventory managers to optimise their stock levels and reduce waste by only ordering what they need.
Data such as designs, samples’ tech packs etc., sent by apparel buyers to the factories come majorly during the night time and factory management starts working on it only the next day and the process of understanding this data consumes whole 24 hours. Deploying RPA lets factories not waste these 24 hours as it’s working 24X7 to accept data and analyse it further to come up with a certain set of information directly through buyers’ PLM software, improving lead time significantly.
India’s largest apparel manufacturing company Shahi Exports also leans onto Robotic Process Automation as well as other automation tools in its digitalisation journey. Shahi has self-prepared some RPA bots, which the company fondly calls Shahi Bots, which have taken over many repetitive, rule-based and predictable (RRP) processes and liberated logistics, marketing and finance teams from menial data entry. On the other hand, Shahi’s computer vision-based solutions recognise faces, vehicles and operations to ensure the highest accuracy in various compliances in the CTPAT area, visitor entries and sewing lines.
In the words of Puneesh Lamba, Chief Technology Officer, Shahi Exports, “Today, our organisation is twice as automated as it was two years ago. As we advance at this pace, we plan to convert many more physical processes into virtual ones. We decided that anything repetitive, rule-based and predictable (RRP) will be the first lot of processes to be automated as they give the best results. I refer to RRP as any process consisting of steps that are repetitive in nature, based on pre-defined rules so that algorithms can be created and are predictable, suggesting the next steps and options which are known. Not only do they free up resources from mundane, monotonous work, but they also give higher efficiency to these mature processes.”
In A Nutshell: Use Cases of RPA in Warehouses
Inventory Management: RPA can help automate the inventory management process in warehouses by monitoring stock levels and reordering products when necessary. This can help reduce the risk of stockouts and improve supply chain management.
Order Processing: RPA can automate the order processing process by extracting information from orders, updating inventory levels and generating shipping labels. This can help warehouses process orders faster and reduce the risk of errors. RPA Bots can also update regarding shipment delays or if the order needs to be cancelled due to any reason. So, they can handle all aspects of order processing.
Data Entry: RPA can help automate the data entry process by extracting data from invoices, receipts and other documents. This can help reduce the risk of errors and improve the accuracy of data entry.
Pick and Pack: RPA can automate the pick and pack process by generating picking lists and packing lists for warehouse workers. This can help reduce the time it takes to fulfil orders and improve order accuracy.
Customer Service: RPA can help warehouses improve customer service by automating the process of responding to customer inquiries and complaints. This can help reduce response times and improve customer satisfaction.
RPA bots’ efficacy in retail
Renowned denim brand Levi Strauss has established itself as a frontrunner in achieving some of its ambitious goals through RPA bots. One of the first bots deployed by the brand has completely digitised how Levi’s invoices wholesale partners. Before February 2021, teams in New Zealand and Australia would download and email monthly statements to the company’s roughly 700 retail partners in the region. Downloading and attaching each individual PDF statement took days to finish. Since deploying an RPA bot that automates the entire wholesale invoicing process, while also improving invoice tracking management in 2021, Levi’s has saved nearly 500 hours of manual work. What took a human more than 5 minutes to do from start to finish now takes 20 seconds with an automated bot.
For the second RPA project, Levi’s has assisted merchandise coordinators (MCs) in the USA and Canada to turn what took multiple days and hours of work spread across roughly five people into one automated bot. To ensure stores have the current season’s products in their systems, MCs have to enter more than 4,000 product codes manually. The process is slow and prone to human errors. After deploying the bot, nearly 750 hours have been saved. With the time saved from this manual data-entry task, MCs are now dedicating it to build other skills.
By 2022, Levi’s had deployed roughly 50 new bots that saved employees more than 25,000 hours a year. One new bot set to have rolled out during 2022 is the Purchase Order (PO) Closure Bot, which has been able to automate and scale the number of POs the finance organisation can close out on time.
“For a company to truly transform digitally, we must approach it from all angles: top-down and bottom-up. We’re ensuring teams across functions have the tools and services they need to work with a digital-first mindset. We are seeing not only an immediate reduction in operational costs but also increased employee satisfaction as teams can focus on higher-value activities. While RPA is common among tech and digital-native companies, it’s just beginning in the retail industry,” commented Harmit Singh, CFO, Levi’s.
Suppliers of Robotic Process Automation (RPA)
There are several suppliers of Robotic Process Automation (RPA) technologies that can be used for warehouse automation. Some of the top suppliers include:
Blue Prism: A provider of enterprise RPA software that can automate repetitive tasks in the warehouse, such as inventory management and order processing.
UiPath: A provider of RPA software that can automate various warehouse processes such as data entry and inventory tracking.
Automation Anywhere: A provider of RPA software that can be used to automate warehouse processes such as order processing, shipment tracking and data entry.
WorkFusion: A provider of intelligent automation software that can automate warehouse processes such as inventory management, order fulfilment and supply chain analytics.
Kofax: A provider of intelligent automation software that can automate various warehouse processes, such as data capture, order processing and shipment tracking.
EdgeVerve: A provider of automation software that can automate warehouse processes such as inventory management, order processing and supply chain analytics.
PegaSystems: A provider of intelligent automation software that can automate warehouse processes such as inventory management, order processing and shipment tracking.
These are just some of the top suppliers of RPA technologies that can be used for warehouse automation.
RPA implementation in Warehouse Management
AJIO: Fashion e-commerce business of India’s largest company Reliance Industries Ltd., is going one step ahead of its competitors in the country. The robotics start-up Addverb has already deployed pick-by-voice software ZESTY in AJIO’s warehouses along with other automated equipment such as robotic conveyors and semi-automated systems. ZESTY, a robotic automation software, electronically gives verbal instructions to operators in the warehouses who, upon activation, go to a specific location. On reaching the location, the operator confirms the location code verbally after which they are told by the software to pick the required quantity!
As many of the warehouses are implementing the RPA bots, the businesses are able to make transition from the nascent stage to the advanced stage in terms of automation adoption as they understand the long-lasting benefits the technology can offer. Right from automation of order processing and payments; automation of email or SMS alerts; automation in communication between the customers; automation of procurement and inventory management processes; generation of service reminders on warehouse equipment using automation; generation of service and road tax reminders using automation; to automating shipment scheduling and tracking with RPA and automation in Finance, RPA has sizeable use cases at warehouse level.
RPA bots can work 24/7 without taking breaks, reducing the time needed to complete tasks. Additionally, robots are less prone to errors compared to humans, which can improve the accuracy of inventory tracking and order processing. By automating repetitive tasks, warehouse employees can focus on more critical tasks such as quality control and customer service.
Going deeper into how RPA bots change the current scheme of things in warehouses
Communication with customers is another challenging task in a warehouse. An open communication channel between the customer and the company is crucial to create trust, and this communication spontaneously can be done through RPA within seconds.
RPA bots take care of typical order-related queries and update customers by querying the system for relevant information. As these bots can be programmed to send premeditated responses which will serve the company’s needs based on query results, the efficiency of the communication is close to perfect.
In an RPA pilot project, Hong Kong’s SF Supply Chain, in association with DHL Logistics, selected ten important warehouse sites as their testing points. They worked with the operations team to analyse the needs of each site, evaluating the overall results and workability. In an SF Supply Chain site that handles over 10,000 orders every month, the RPA solution was adopted to manage courier data entry, which was previously handled by two full-time staff. RPA robots handle highly repetitive and time-consuming tasks. The extremely low error attribute of RPA technology also avoids manual operation errors, setting the foundation for higher-quality customer service.
International Data Corporation (IDC), commissioned by Automation Anywhere, states that nearly half of all businesses in India will implement robotic process automation (RPA) by 2024. The study also found that 56 per cent of organisations in the country plan to deploy digital workers and software bots to work directly with their human employees.
Inventory management is another head-hitting task in a warehouse. The companies often find it difficult to manage overstocks and stockouts as both are loss-making situations for a fashion business. The traditional way of handling is a complex and challenging task.
How RPA works in this case? With RPA, the system automatically generates alerts to inventory managers when the stock levels of certain products fall below a certain threshold. This alert triggers the inventory managers to take a viable decision, therefore the amalgamation of both integrated systems works well for inventory management.
Coordination between logistics partners for delivery can also be done effectively with RPA bots. Consider a scenario where an e-commerce retailer receives an order for a product from a customer. The RPA bots in the supply chain system analyse the product’s location and determine which warehouse has the item in stock. The bots then assign an optimal logistics partner based on variables such as destination, cost, capacity and lead time. The bots ensure that the order is processed efficiently by coordinating between the various logistics partners, such as road freight and last-mile delivery services, to ensure that the product reaches the customer within the specified timeframe.
Inventory management system led by RPA predicts a surge in demand for a particular product during a certain season. The inventory managers can order more of that product in advance to meet the demand and avoid running out of stock.
Technical hurdles in RPA bots’ implementation are predicted to be short-lived
RPA implementation comes with its own set of challenges, such as data quality and integration with existing systems. Poor data quality can create errors in orders and cause disruption in the supply chain. It is thus necessary to have solid data processes in order for bots to use accurate information. Additionally, incorporating RPA into complex supply chain management systems that have been customised over time requires careful planning and coordinated testing to prevent any disruptions to the system. On top of this, the potential cybersecurity risks associated with widespread RPA adoption must be addressed by investing in robust security measures against unauthorised access or manipulation of the bots.
Even though challenges are there but adoption of RPA is increasing. Companies like Zara, AJIO, Levi’s, Flipkart, Raymond and Amazon are welcoming it with open arms. Furthermore, companies that invest in robust cybersecurity measures and establish sound data processes can reap the significant benefits of RPA making it a valuable tool for their operations and business growth.